Never use liquid threadlockers on any electrical fixings!
02 May 2018
‘Threadlocking’ means preventing threaded fixings from loosening due to vibration. There are many mechanical ways to do this, including split pins, locking nuts, special washers, etc., but the term ‘threadlockers’ is usually applied to chemical products that glue a thread in place.
Liquid threadlockers have become quite popular, because they reduce the parts inventory, are easy to apply, and low-cost.
Unfortunately, in my experience they can be used carelessly, creating big problems for safety and EMC, and that is what this brief article is about.
Examples of liquid threadlockers include ‘red’ and ‘blue’ products from Loctite (http://henkeladhesivesna.com/blog/the-difference-between-red-blue-green-and-purple-threadlockers) and it has become quite common for people to use the word ‘Loctite’ to mean a chemical threadlocker. It’s like calling all facial tissues ‘kleenexes’, or all vacuum cleaners ‘hoovers’.
The problem is that all liquid chemical threadlockers are insulators, and because they have low viscosity and cover most/all of the thread, they ruin any electrical or radio frequency (RF) bonding that a fixing might be supposed to provide.
A few years ago I was working on a product that used a 4mm diameter screw thread as protective conductor (“safety earth”) connector. The entire protective conductor circuit is supposed to measure less than 0.1 Ohms, but this one screw connection alone was 8 Ohms! I noticed that it was coated with something red, which I presumed was a liquid threadlocker. After I scraped it all off, the fixing measured under one milliohm, instead of 8 Ohms!
Clearly, using liquid threadlocker on any screwed/bolted electrical connections is very bad, and quite possibly illegal and unsafe too.
Note: There is a conductive liquid product made by Loctite, but it is an epoxy adhesive – not a threadlocker. I often hear people suggest using ‘conductive Loctite’, when what they really mean is conductive threadlocker, but as far as I have ever been able to discover no-one makes (or ever has made) a conductive liquid thread-locking products. I imagine the addition of the necessary conductive fillers would make the viscosity too high for a threadlocking product.
Of course, a high resistance in any RF-bond will ruin it, just as surely as it will ruin an electrical safety connection.
If you read my articles you will know that, for both electrical safety and RF bonding, I always recommend not relying on screw threads because of the likelihood of corrosion. Instead, the screw fixing should be used to press two conductive surfaces together to create the electrical, electrical safety, or RF bond.
Unfortunately, unless the amount of liquid threadlock is precisely metered every time it is applied to an individual screw thread, there is the risk of it not providing sufficient protection from vibration – so people always over-apply it, to make sure that they get reliable antivibration. The result is that the excess insulating liquid just gets everywhere – including inbetween the conductive surfaces that are being clamped together by the fixing!
In a recent military project, I found that the over-liberal use of liquid threadlocker had caused it to squirt into a joint in a shielded enclosure at every screw fixing (and there were a lot of them!). It not only prevented the screw threads from providing RF-bonds across the shielding joint, but also prevented to two metal enclosure halves from making direct contact with each other! The shielding that was achieved by the enclosure was terrible, useless.
As conductive liquid threadlockers don’t exist, what can we use for locking threads without having to use precisely metered doses or extra parts?
Well, Nylok nuts and bolts, https://nylok.com, use a solid ring of nylon that is cut into by the thread to provide the thread locking function. They have been readily available for over 40 years to my knowledge, and are available compliant with a huge range of military / avionics / aerospace specifications.
Loctite offer a solid threadlocker that they call ‘Dri-Loc’, www.threadlocking.co.uk/loctite-dri-loc.html. Unlike Nylok’s standard off-the-shelf fixings, Dri-Loc is applied by fixing suppliers as a custom solution (I assume under licence from Loctite or Henkel).
Another alternative is Stanley’s ‘Spiralock’, www.stanleyengineeredfastening.com/brands/spiralock which achieves about 15% more torque than regular screw threads or coil inserts, and provides antivibration threadlocking without any additional materials.
Spiralock products are re-usable, whereas liquid or solid threadlockers can only be used once. (Nylok products are sometimes re-used, although they shouldn’t be. I understand that in the UK military during wartime, re-using a Nylok nut or bolt is a court-martial offence!).
Spiralock fixings are made to order, and special materials are available (e.g. non-sparking).
So far I have only been discussing threadlocking for antivibration. But all threaded fixings (screws, nuts, bolts, etc.) allow air, liquids, fine dusts and RF surface currents to leak spirally along their screw threads and ruin environmental sealing and RF shielding.
Also, you may be surprised to learn that all regular thread types do not properly centre in their hole, so their screw heads all sit at a slight angle to the surface they are fixing. So their heads all leak too!
We can prevent this environmental and RF leakage by screwing fixings into blind threaded holes, so that the screw thread doesn’t penetrate all the way through the joint. Or we can use washers made of a tough conductive and environmental gasket material (e.g. www.kemtron.co.uk/emc-shielding-solutions/woven-expanded-wire-in-elastomers) under the screw heads.
But we would prefer to achieve antivibration, environmental sealing and RF shielding without having to add any other parts, even washers.
Spiralock screws are self-centring, so their screw heads do sit flat on the surface they are fixing. We still can’t rely on their screw heads to make such a perfect fit, every time, to ensure environmental and RF sealing – but an interesting possibility is to use Spiralock screws with an 87°underhead feature that guarantees a continuous-metal-ring contact between the screw’s head and the surface it is fixing. Re-usable threadlocking (antivibration), some degree of waterproofing (I have seen IP7 quoted), and RF shielding – all without any additional parts or materials! Interesting.
Get more from EMC Standards
EMC Standards is a world-leading resource for all things EMC and EMI related. Our website is packed full of both free and paid-for content, including:
- Online quiz
- Webinars
- Training quiz
- And much more!
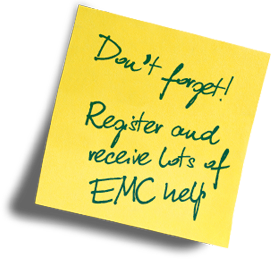
Electromagnetic Engineering (EMgineering) is the basis for proven good design practices for signal integrity (SI), power integrity (PI), and the control of EMI emissions and immunity (EMC).
Our aim is to help people learn how to more quickly and cost-effectively design and manufacture electronic equipment (products, systems, installations, etc.) to meet functional (i.e. SI/PI) specifications and conform to EMC standards, directives and other requirements.
Such equipment should benefit from reduced warranty costs and financial risks, whilst improving uptime, competitiveness and profitability.
We also cover basic good electrical safety engineering; and the Risk Management of Electromagnetic Disturbances / EMI, whether for Functional Safety or other types of risk.
Join EMC standards TODAY!