Complying with EU Safety Requirements
23 Nov 2018
Passing tests to the most relevant LVD harmonised standard isn’t enough to comply with EU Safety Requirements
(Similar arguments apply to EU Directives other than the LVD, e.g. Machinery, Medical, Personal Protective Equipment, etc.)
There are two important issues here:
Firstly, the EU's Product Liability Directive (PLD) -which is not a CE-marking directive – simply requires products to be as safe as people generally have the right to expect. It has been updated by Directive 99/34/EC.
The EU's PLD is implemented in UK law as the Consumer Protection Act (CPA), updated by the Consumer Rights Act, but by 'consumer' it includes business customers too, including products used by professionals for their work, and 3rd parties (e.g. people who are nearby).
There are only two effective legal defences against a lawsuit under these regulations – one is that the product complied with the state of the art in safety at the time of supply; the other is that an appointed official told you to design your product in the unsafe way. There are some national variations within the EU on the detailed interpretations, discussed here.
Unpacking the ‘state of the art’ defence: it is important to note that the word ‘product’ means each individual unit of production, and not a product type or model.
Also important, is that the laws apply when the product was made available to customers, end-user, etc., in the EU – not the date when the final design of the product type or model was signed off for manufacture.
Compliance with the safety requirements therefore means maintaining a high-level of activity in the (continuously developing) level of safety that people generally expect, and in the (continuously developing) state of the art in safety engineering, throughout the manufacturing, storage and shipping stages of a product’s lifecycle. The safe design of a product does not finish until the very last unit has been shipped!
(And even that may not be the end of a manufacturers legal obligations on safety, because of the EU’s General Product Safety Directive, implemented in the UK as the General Product Safety Regulations, which requires them to be responsible for their products’ safety after supply to customers or end-users – a subject for a future blog.)
It is also notable that the entity held liable under the PLD is the ‘producer’ of the product, which means the manufacturer of a finished product, the producer of any raw material or the manufacturer of a component part, and any person who – by putting his name, trade mark or other distinguishing feature on the product – presents himself as its producer.
Some member states have limited the maximum penalties that can be awarded in civil lawsuits under the PLD to 70 Billion Euros (yes, Billion, not a typo!), whereas others – like the UK – have not set any limits at all. This amount is so very high to make even the largest companies in the world think twice about exposing customers, end-users, and 3rd parties in the EU to unacceptable levels of safety risk.
Not complying with the PLD presents much greater legal/financial risks than not complying with the LVD.
The PLD is not a ‘CE-marking directive’ so has no corresponding Declaration of Conformity, but every product that is offered for sale in the EU is required by EU/UK law to comply with the PLD anyway. Effectively, offering a product for sale is a declaration of conformity to the PLD.
There are no harmonised (or other) standards published under the umbrella of the PLD. Good safety engineering in accordance with the state of the art is required.
These days this means using a comprehensive hazard identification and risk assessment from the start of a project to guide its design. This will determine what hazards could reasonably foreseeably exist, then what their likelihoods are, leading to a risk level and comparison with acceptable levels to establish whether each individual risk needs to be reduced, and by how much.
Risks needing reduction will then apply any number of relevant standards or other kinds of publications. Where these don’t reduce a risk by enough (which is not unusual, because technology is typically a decade ahead of the safety standards developed for it), it may be necessary to develop new safety design techniques.
A hazard identification and risk assessment must be a ‘live’ document that guides safety design and other activities throughout the entire lifecycle of a product. It is most definitely not just an FMEA, FMECA or similar design analyses conducted after the design is complete! Several different types of design analyses are used to help verify/validate individual risk-reductions as part of an overall hazard identification and risk assessment, and none of them are considered to be sufficient on their own.
Secondly, the latest version of the Low Voltage Directive (LVD) is 2014/35/EU, and – like all the Directives published under the New Legislative Foundation, which some have called ‘The EU Single Market Version 2’ – it requires a hazard identification and risk assessment to be used as the basis for all compliance activities.
To comply with the state of the art in safety, means being aware that better (safer) alternatives may exist in other safety standards, or other documents of any type, and applying them if the risk assessment requires it.
Simply passing tests to the single most relevant standard is not sufficient any more, under the LVD.
Even if your product’s design passes all the tests under the most relevant safety standard, if it is found to be unsafe in some way it can be banned from the entire EU. And if its flaw has caused anyone to be injured or killed, or caused significant property damage, the legal damages in civil lawsuits under the PLD can be absolutely enormous.
(As far as I know, no-one has ever brought a civil lawsuit under the LVD, although I am told that the law does not forbid it. But the possible claims are much higher in the case of the PLD/CPA, and the opportunities for defendants to wriggle out via legal loopholes is much smaller.)
Of course, we never want to be involved in any lawsuits at all, because even if we win we can still be bankrupted by the legal fees. And even if we can afford the legal fees we usually can't afford to have our senior personnel tied up with fighting such issues for the months/years (even decades) that can be required.
So the best idea, the least financially risky approach, is to follow a proper risk management approach along the lines broadly described earlier, that covers all of the hazards and their risks regardless of which standards are used.
I have been teaching this approach to safe design of electrical/electronic products since the mid-1990s, recommending it to people to minimise their time, costs and risks, while most manufacturers were taking the easy way out by choosing to assume that simply passing tests to the single most-relevant safety standard was sufficient.
Of course, it never was sufficient for the PLD, but because the PLD does not require a Director to sign a Declaration of Conformity – even though it has been EU and UK Law since 1987 – most manufacturers were not aware of it! I was even once told by a company Director that he wanted to remain unaware of safety laws because then he could use the defence that he didn’t know about them. (Yeah, right! Like that’s going to work in a court of law! It can’t even defend against a speeding ticket.)
But now that the LVD, 2014/35/EU, requires a documented hazard identification and risk assessment, and makes clear that sticking with the most-relevant standard might well not be sufficient, the LVD has finally aligned itself with the PLD and with my original design and training approach!
Get more from EMC Standards
EMC Standards is a world-leading resource for all things EMC and EMI related. Our website is packed full of both free and paid-for content, including:
- Online quiz
- Webinars
- Training quiz
- And much more!
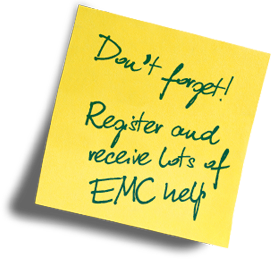
Electromagnetic Engineering (EMgineering) is the basis for proven good design practices for signal integrity (SI), power integrity (PI), and the control of EMI emissions and immunity (EMC).
Our aim is to help people learn how to more quickly and cost-effectively design and manufacture electronic equipment (products, systems, installations, etc.) to meet functional (i.e. SI/PI) specifications and conform to EMC standards, directives and other requirements.
Such equipment should benefit from reduced warranty costs and financial risks, whilst improving uptime, competitiveness and profitability.
We also cover basic good electrical safety engineering; and the Risk Management of Electromagnetic Disturbances / EMI, whether for Functional Safety or other types of risk.
Join EMC standards TODAY!