'Accidental antennas' and good Electromagnetic (EM) Design
06 Sep 2018
FACTS:
- All conductive structures, whatever their intended purpose, behave as accidental transmitting and receiving radio antennas. Whether we want them to or not.
- I.e. The voltages and currents in any/all conductive structures, whatever their intended purpose, interact with their local electromagnetic (EM) fields. Whether we want them to or not.
- It’s what any/all conductors do, and there’s simply nothing we can do about it!
- This applies equally to stray/parasitic voltages and currents coupled via near-fields from nearby circuitry; and to the voltages and currents picked up from far-fields from intentional transmitters such as radio, TV, cellphone, WiFi, Bluetooth, etc.
- This applies equally whether the conductive structures are intended to carry currents in a circuit, or not – for example if they are metal or metallised parts of enclosures (even parts of mostly plastic enclosures); decorative metal trim; hydraulic, pneumatic, gas or water piping (if metal); metal support structures, etc.
- This applies equally to conductive liquids (e.g. blood, saline, sea water, etc.) inside insulating pipes.
- All clocked digital ICs, such as microprocessors; ASICs and SoCs containing microprocessors, and FPGAs, now emit broadband differential-mode noise currents from all pins that toggle repetitively.
And they emit broadband common-mode noise currents from every single one of all their pins, including all input pins, power pins, ‘static’ output pins, analogue I/O pins, and (so-called) Ground pins.
These frequencies typically extend from half their system clock frequency or lower, all the way up to 6GHz (or higher). They will extend to higher frequencies in future. - At up to 6GHz, even conductive structures as long as 12.5mm (half an inch) if insulated by air, or 6.35 mm long (a quarter of an inch) if inside an FR4 PCB, can behave as very effective ‘resonant accidental antennas’.
CONSEQUENCES:
- Accidental antennas created by conductive structures (whatever their intended functions) in products containing clocked digital ICs, such as microprocessors; ASICs and SoCs containing microprocessors, and FPGAs, cause difficulties for complying with EMC emissions and immunity test standards.
For the same reasons, these accidental antennas cause/suffer EMI in real-life applications, making it difficult to achieve good functional performance, low warranty returns, good customer perceptions and high levels of repeat sales. (Which is what passing EMC tests is all about, really!) - To ensure that a conductive structure, whatever its intended purpose, is not an efficient accidental antenna, it should not have any dimension larger than one-tenth of a wavelength at the highest frequency of concern.
For up to 6 GHz, this means 5.0 mm if the conductors are insulated by air, or 2.5 mm if they are insulated by FR4 PCB material. - To be a very inefficient accidental antenna, a conductive structure should not have any dimension larger than one-hundredth of a wavelength at the highest frequency of concern.
For 6 GHz this means 0.5 mm if insulated by air, or 0.25 mm if insulated by FR4 PCB material. Note that this is less than the length of a typical via hole in a PCB! - To comply with the toughest military or automotive EMC specifications, even conductors that smaller than one-hundredth of a wavelength long at the most critical frequencies, could easily be still too efficient as accidental antennas.
- Designing and manufacturing products that contain clocked digital ICs, such as microprocessors; ASICs and SoCs containing microprocessors, and FPGAs, therefore requires close attention to very small structural details, which generally increases the overall cost of manufacture.
SOLUTION:
- Don’t let higher-than-necessary noise frequencies into parts of the product that don’t need them.
This will allow good EMC to be achieved for those parts without having to control extremely small structural details, helping to reduce the overall cost of manufacture of the product. - Another way of looking at this, is say that we restrict the highest frequency noises, whether they are differential-mode or common-mode, to the parts of the product that actually need to use such high frequencies.
This minimises the need to control very small structural details, helping to reduce the overall cost of manufacture of the product. - So, for example, in well-designed and cost-effective products, we generally see:
- Noise frequencies up to several GHz being contained to small PCB areas by the use of PCB-mounted filtering and shielding. Within those areas, very careful attention is paid to every conductive feature larger than, say, 0.1mm at present (less in future).
- Noise frequencies up to (say) 100 MHz are contained within other board areas, again by using PCB-mounted filtering and shielding. Within these areas, very careful attention must be paid to every feature larger than about 5mm.
- Baseband analogue circuits on the PCB are filtered and shielded to restrict the noise frequencies they experience from digital and switching power circuits elsewhere on the board, to their highest frequency for which they behave linearly.
This is typically no more than about 50 kHz, but data sheets don’t provide any useful information on this frequency, so it must be measured (easy to do on a regular test bench). - Shielded cables external to a product are limited by filtering and shielding to carrying signals or power at noise frequencies up to what their shielding layers and connectors can deal with.
- Unshielded cables external to a product are limited to noise frequencies from digital and switching power circuits up to 10kHz (less, for some military or aerospace applications), by the use of shielding and filtering at the level of the overall product enclosure.
BACKGROUND and DETAIL:
For more detail on this topic, log-in as a Member at www.emcstandards.co.uk/login and view my webinar posted at: www.emcstandards.co.uk/go-emgineering-si-pi-emc-webinar-1d. (If not already a member, register for free at www.emcstandards.co.uk/login.)
I have also published the material in this new webinar as an article in In Compliance magazine: www.emcstandards.co.uk/files/introduction_to_em_engineering_incompliance_july_2017_as_published.pdf.
The material in the webinar/article above is a recent addition to ‘Physics/Basics of EMC’ material I have made available during the last eighteen years as:
- three free webinars: www.emcstandards.co.uk/webinars2
or www.emcstandards.co.uk/understanding-emc-basics-a-3-part-series
- a free magazine article: www.emcstandards.co.uk/files/the_physical_basis_of_emc_5_april_2010.pdf
- an inexpensive textbook: www.emcstandards.co.uk/the-physical-basis-of-emc2.
However, for the best and most up-to-date understanding on this topic, purchase the latest version of my training course notes: www.emcstandards.co.uk/the-physical-basis-of-si-pi-and-emc.
Get more from EMC Standards
EMC Standards is a world-leading resource for all things EMC and EMI related. Our website is packed full of both free and paid-for content, including:
- Online quiz
- Webinars
- Training quiz
- And much more!
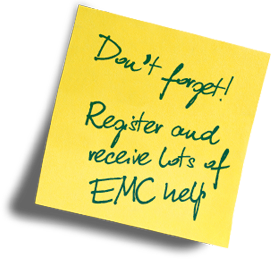
Electromagnetic Engineering (EMgineering) is the basis for proven good design practices for signal integrity (SI), power integrity (PI), and the control of EMI emissions and immunity (EMC).
Our aim is to help people learn how to more quickly and cost-effectively design and manufacture electronic equipment (products, systems, installations, etc.) to meet functional (i.e. SI/PI) specifications and conform to EMC standards, directives and other requirements.
Such equipment should benefit from reduced warranty costs and financial risks, whilst improving uptime, competitiveness and profitability.
We also cover basic good electrical safety engineering; and the Risk Management of Electromagnetic Disturbances / EMI, whether for Functional Safety or other types of risk.
Join EMC standards TODAY!